塗(tú)層技術及(jí)工藝流程塗層技術及工藝流程塗層技術及工藝流程塗層技(jì)術及工藝流程 1.真空塗層技術的發展 真空塗層技(jì)術起步時間不長,國際上在上世紀六十年代才出現將CVD(化學氣相沉積)技術應用於硬質合金刀具(jù)上。由於 該技術需在高溫下(xià)進行(工藝溫度高於 1000ºC),塗層種類單一,局限性很大,因(yīn)此,其發展初期(qī)未免(miǎn)差強人意。 到了上世紀七十年代末,開始出現 PVD(物(wù)理氣相沉積) 技術,為真空塗層開創(chuàng)了一個充滿燦爛(làn)前景的新天地,之後在短短的二、三十年間PVD 塗層技術得到迅猛(měng)發(fā)展,究其原因,是因(yīn)為其在真空密封的腔體內成(chéng)膜,幾乎無任何環境汙(wū)染問題,有利於環保;因為其能得到光亮、華貴的表麵,在顏色上(shàng),成熟的有七彩色、銀色、透明色、金黃色、黑色、以及由金黃(huáng)色到黑色之(zhī)間的任何一種顏色,可謂五(wǔ)彩繽紛,能夠滿足裝飾性的各種需要;又由於 PVD 技(jì)術,可以輕鬆得到其他方法難以獲得的高硬度、高耐磨性的(de)陶瓷塗層、複合塗層,應用在工裝(zhuāng)、模具上麵,可以(yǐ)使壽命成倍(bèi)提高,較好地實現了低成本、高收益的效果;此外, PVD 塗層技術具有低溫、高能兩個特點,幾乎可以在(zài)任何基材上成膜,因此,應用範圍十分(fèn)廣闊,其發展神速也就不(bú)足為奇。 真空塗層技術發(fā)展到(dào)了今天還出(chū)現了PCVD(物理化學氣(qì)相沉積)、MT-CVD(中溫化學氣相沉積(jī))等新技術(shù),各種塗層設備、各種塗層工藝層出不窮,如今(jīn)在這一領域中,已呈現出百花齊放,百家爭鳴的喜人景象。 與此同時,我們還應(yīng)該清醒地看到,真空塗層(céng)技(jì)術的發展又(yòu)是嚴重不平衡的。由(yóu)於刀具、模具的工作環境極其惡劣,對薄膜附著力的要求,遠高於裝飾塗層。因而,盡管裝飾塗層的廠家已(yǐ)遍布各地,但能夠生產工模塗層的廠家並不多。再加(jiā)上刀具、模具塗層售(shòu)後服務的欠缺,到目前為止,國內大(dà)多數塗層設備廠家都不能提供完整的(de)刀具塗層工藝技術(包括前處理工藝、塗層(céng)工藝、塗後處理工藝、檢測技術、塗層刀(dāo)具和模具的應用技術等),而且,它還(hái)要(yào)求工藝技術人員,除了精通塗層的專業知識以外,還應具有紮實的金屬材料與熱處理知識、工模塗層前表麵(miàn)預處(chù)理知識、刀具、模具塗層的合(hé)理選擇以及上(shàng)機(jī)使用的技術 要求等,如果任一環節出現問(wèn)題,都會給使用者產生使用(yòng)效果不理想這樣的結論。所有這些,都嚴重製約了該技術在刀具、模具(jù)上的應用。 另一方麵,由(yóu)於該技術是一門介乎材料學、物理學、電子、化學等學(xué)科的新興邊緣學科,而(ér)國內(nèi)將其應用於刀具、模具生(shēng)產領域內的為數不多的幾個骨幹廠家,大(dà)多走(zǒu)的也是一條從國外引(yǐn)進先進設備和工藝技術的路子,尚需一個(gè)消化、吸收的過程,因此,國內目前在該領域內的技術力量與其發展很不(bú)相稱,急需奮起直追(zhuī)。 2. PVD 塗層的(de)基本概念(niàn)及其特點 PVD 是英文“Physical Vapor Deposition”的縮寫形式,意(yì)思是物理氣相沉(chén)積。我們現在一般地把
真空蒸鍍、濺射鍍膜、
離子鍍等都稱為物理氣相沉積。 較為成熟的 PVD 方(fāng)法主要有多弧鍍與磁控濺射鍍兩種方式。多弧鍍設備結構簡單,容易操作。它的離(lí)子蒸發源靠(kào)電焊機電源供電即可工作(zuò),其引弧的過程也與電焊類似,具體地說,在一定工藝氣壓下,引弧針(zhēn)與蒸發離(lí)子源短(duǎn)暫接觸,斷開,使(shǐ)氣體放電。由於多弧鍍的成因主要是借助於不斷移動的弧斑,在蒸發源表麵上連續形成熔池,使金屬蒸發後,沉積在基體上而得到薄膜層的,與磁控濺射相比,它不(bú)但有靶材利用率高,更具有金屬離子離化率高(gāo),薄膜與基體之間結合(hé)力(lì)強(qiáng)的優點。此外,多弧鍍塗層顏色較為穩定,尤其是在做 TiN 塗層時,每一批次均容易得到相同穩定的(de)金黃色,令
磁控濺射法望塵莫及。多弧鍍的不足之處是,在用傳統的(de) DC 電源(yuán)做低溫塗層條(tiáo)件下,當塗層厚度(dù)達到(dào)0.3μm 時,沉積率與反射率接近,成膜變得非常困難。而且,薄膜表麵開始變朦(méng)。多弧鍍另一個不足之處是,由於金屬是熔後蒸發,因此沉積顆粒較大,致密度低,耐磨性比磁控濺射法成膜差。 可見,多弧鍍膜與磁控濺射法鍍膜各有(yǒu)優劣,為(wéi)了盡可能地發(fā)揮它們各自的優越(yuè)性(xìng),實現互補,將多弧技術(shù)與磁控技術合(hé)而為一的塗層機應運而(ér)生。在工藝上(shàng)出現了多弧鍍打底,然後利用磁控濺射法增厚塗層,最後再利用多弧鍍達到最(zuì)終穩定的表(biǎo)麵塗層顏色的新方法。 大約(yuē)在八十年代中後(hòu)期,出現了熱陰極電子槍(qiāng)蒸發離子鍍、熱陰(yīn)極弧磁控等離子鍍膜機,應用效果很好,使TiN 塗層(céng)刀具很快得到普及性應用。其中熱陰極電子槍蒸發離子鍍,利用銅坩堝加熱融化(huà)被鍍金屬材料(liào),利用鉭燈絲給工(gōng)件(jiàn)加熱、除氣,利用電子槍增強離化率,不但可以得到厚度 3~5μm的TiN 塗層,而且其結合力、耐磨性均有不俗表現,甚至用打磨的方法都難以除去。但是這些設備都隻適合於 TiN塗層,或純金屬薄膜。對於多元塗層或(huò)複合塗層,則力(lì)不(bú)從心,難以適應高硬度材料(liào)高(gāo)速切 削以及模具應用多樣性的要求。 3. 現代塗層(céng)設備(均勻加熱(rè)技術、溫度測量技(jì)術、非(fēi)平衡磁(cí)控濺(jiàn)射技術、輔助陽極技術、中頻電源、脈衝技術) 現代塗層設(shè)備主(zhǔ)要由真空室(shì)、真空獲得部分、真空測量部分、電源供給部分、工藝氣體輸(shū)入係統、機械傳動部(bù)分、加熱及測溫部件、離子蒸發或濺射源、水冷係統等部分組成。 3.1 真空室 塗層設備主要(yào)有連續(xù)塗層生產線(xiàn)及單室塗層機兩(liǎng)種形式,由於工模塗層對(duì)加熱及機械(xiè)傳動部分有較高要求,而且工模形狀、尺寸千差萬別,連續塗層生產線通常難以滿足要求,須采用單室塗層機。 3.2 真空獲得部分(fèn) 在真空技術(shù)中,真空獲得部分(fèn)是重要組成部分。由於工模件塗層高附著力的要求,其塗層工藝開始前背景真空度最好高於6mPa,塗層工藝結束後真空度甚至可達(dá) 0.06mPa 以上,因此合理選(xuǎn)擇真(zhēn)空獲得設備,實現高真空度至關重(chóng)要。 就目(mù)前來說,還沒有一種泵能從大氣壓一直工(gōng)作到(dào)接近超高真空。因此,真空的獲(huò)得不是一種
真空(kōng)設備和方法所能達(dá)到的,必須將幾種(zhǒng)泵聯合使用,如機械泵、分子泵係統等。 3.3 真空測量部分 真空係統的真空測量部分,就(jiù)是要對真空室內的壓強進行測量。像真空泵一樣,沒有一種真空(kōng)計能測量整個真空範圍,人們於是按不同的(de)原理和要求製成了許多種類的真空計。 3.4 電源供(gòng)給部分靶電源主要有直流電源(如 MDX)、中頻電(diàn)源(如美國 AE公司生產的 PE、PEII、PINACAL);工件本身通常需加直流(liú)電源(如(rú) MDX)、脈衝電源(如美國AE公司生產的(de) PINACAL+)、或(huò)射頻(pín)電源(RF)。 3.5 工藝氣體輸入係統(tǒng) 工藝氣(qì)體,如氬氣(Ar)、氪氣(Kr)、氮氣(N2)、乙炔(C2H2)、甲烷(CH4)、氫氣(H2)、氧氣(O2)等,一般均由氣瓶供(gòng)應,經氣體減壓閥、氣(qì)體截止閥、管路(lù)、氣體(tǐ)流量(liàng)計(jì)、電磁閥、壓電閥(fá),然後通(tōng)入(rù)真空室。這(zhè)種(zhǒng)氣體輸入係統的優點是,管路簡捷、明快,維修或更換氣瓶容易(yì)。各塗層機之間互不影響。也有多台塗層機共用一(yī)組氣(qì)瓶的情況,這種情況在一些(xiē)規模較大的(de)塗層車間可能有(yǒu)機會看到。它的好處是,減少氣瓶占(zhàn)用量,統一規劃、統一布局。缺點是,由於接(jiē)頭增多,使漏氣機會增加。而且,各塗層機之間會(huì)互相(xiàng)幹擾,一台塗層(céng)機的管路(lù)漏氣,有可能會影響到(dào)其他塗層機的產品質量。此外,更換氣瓶時,必須保證所有主機都處於非用氣狀態。 3.6 機械傳動部分 刀(dāo)具塗層要求周邊必須厚度均勻一致,因此(cǐ),在塗層過程中須有三個轉動量才能滿足要求。即(jí)在要求大(dà)工件台轉動(I)的同時,小的工件承載台也轉動( II),並且工件本身還能同時自轉(III)。 在機械設計上,一般是(shì)在大工件轉盤底部中央為一大的主動(dòng)齒輪,周圍是一些小(xiǎo)的星行輪與之齧合,再用撥(bō)叉撥動工件自轉。當然,在做模(mó)具塗層時(shí),一般有兩個轉動量就足夠了,但是(shì)齒輪可承載量必須大大增強。 3.7 加熱及測溫(wēn)部分 做工模塗層的時候(hòu),如何(hé)保證被(bèi)鍍工件均勻加熱比裝飾塗 層加熱(rè)要重要(yào)得多。工(gōng)模塗層設備一般均有前後(hòu)兩個加熱器,用熱電偶測(cè)控(kòng)溫度(dù)。但是,由(yóu)於熱電偶裝夾的為置不同,因而,溫度讀數不(bú)可能是工件的真實溫度(dù)。要想測得工件的真實溫(wēn)度,有很多方法,這裏介紹一種簡便易行的表麵溫度計法 (Surface Thermomeer)。該溫度計的工作原(yuán)理是,當溫度計受熱,底部的彈簧將受熱膨脹,使(shǐ)指針推動定位指針旋轉,直到最(zuì)高溫度。降溫的時候,彈簧收縮,指針反向旋(xuán)轉,但定位指針維持在最高溫度(dù)位置不動(dòng),開門後,讀取定位指針指示的溫度,即為真(zhēn)空室內加熱時,表(biǎo)麵溫度計放置位置所(suǒ)曾(céng)達到的最高溫度值。 3.8
離子蒸發及濺射源 多弧鍍的蒸發源(yuán)一般為圓餅形,俗稱圓餅靶,近幾年也出現了長方形的多弧靶,但(dàn)未見有明顯(xiǎn)效果(guǒ)。圓餅靶裝在銅靶(bǎ)座(陰極座(zuò))上麵,兩者為羅紋連接。靶座中裝有磁鐵,通過前後移動磁鐵,改變磁場強度,可調整弧(hú)斑移動速度及軌跡(jì)。為了降低(dī)靶及靶座的溫度,要給靶座不斷通入冷卻水。為了保證靶與靶座之間的高導電、導熱性,還可以在靶與靶(bǎ)座之間加錫(Sn)墊片。磁(cí)控濺射鍍膜一般采用(yòng)長方形或圓柱形靶材, 3.9 水冷係統(tǒng) 因為工模塗層時,為了提高金(jīn)屬(shǔ)原子的離化率,各個陰(yīn)極靶座都盡可能地采用大的功(gōng)率輸出,需要充分冷卻;而且,工模塗層(céng)中的許多種塗(tú)層,加(jiā)熱溫度為 400~500ºC,因此,對(duì)真空室壁、對各個密封麵(miàn)的冷卻也很(hěn)重要,所以冷卻水最好采用18~20ºC 左(zuǒ)右的冷水機供水。為了防止(zhǐ)開門後,低溫(wēn)的(de)真空室壁、陰極靶與熱的空(kōng)氣接觸析出水珠,在開門前 10 分鍾左右,水冷係統應有能力切換到供(gòng)熱水狀態,熱水溫度約為 40~45ºC。 4. 工模具PVD 的工作步驟 工模具 PVD 基本工藝流程可簡述為:IQC→前處理→PVD→FQC,分別介紹如後。 4.1 IQC IQC(In Quality Control)的主要工作除了常規的清點數量(liàng) , 檢查圖紙與實物是否相符外,還須仔細檢查工件表麵,特別是刃口(kǒu)部位(wèi)有無裂紋等缺陷。有時對於一些刀具、刀粒的(de)刃口,在體式顯微鏡下觀察,更方便發現問題;另外,IQC 的人員還要注(zhù)意(yì)檢查待鍍膜件有無塑膠、低熔點(diǎn)的焊料等,這些東西如果因漏(lòu)檢(jiǎn)而混入鍍膜程序,則將在真空室內嚴重放氣,輕者造成整批產品脫塗層,重者使原本 OK 的產品報(bào)廢,後果不堪設想。 4.2 前(qián)處理工藝(蒸汽槍、噴砂、拋光、清洗) 前處理的目的是淨化或粗化工件表麵。淨化就是要(yào)去除各種表麵玷汙物(wù),製備潔淨表麵。通常使用各種淨化(huà)劑,借(jiè)助機械、物理或化學的方法進行淨化。 粗化與(yǔ)光蝕相反,其目的在(zài)於製備粗糙的表麵以提高噴塗層或塗料裝飾的結構強(qiáng)度。我們現在已有的前處理主要方法(fǎ)為:高溫蒸洗、清(qīng)洗、噴(pēn)砂、打(dǎ)磨(mó)、拋光(guāng)等方法。 4.2.1 高溫蒸洗 目前,PVD 車間常用的高(gāo)溫蒸洗設備是蒸汽槍。它的最大工作溫(wēn)度可達(dá) 145?C,氣壓在 3~5 巴左右。由於模具中經常帶有一(yī)些細小孔、螺紋孔,孔內中常常有油汙、殘餘冷卻液等雜質(zhì),用常規清(qīng)洗的方法難以除去(qù)。此時,高溫蒸洗設備(bèi)便可最大(dà)程度的發揮它的(de)優越性(xìng)。
4.2.2 清洗 各廠工模塗(tú)層前清洗程序大(dà)致(zhì)如下: 1.超聲波除蠟→2.過水→3. 超聲波除油→4.過水→5. 超聲波自換(huàn)→6.過水(shuǐ)→7.過純水→8.強(qiáng)風幹燥 具體實施時,與我們所熟(shú)悉的裝飾塗層(céng)前的清洗又有許多不同。這(zhè)是(shì)因為裝飾塗層的底材大多為不(bú)鏽鋼或鈦合金,不容易生鏽。此外,裝飾塗層對水印、點(diǎn)痣等缺陷是絕(jué)對(duì)不允許的。因此,裝飾塗層對(duì)純水的(de)水質(zhì)要求極高,甚至(zhì)要達到 15MΩ 以上。要保(bǎo)證清洗的高質量(liàng),可以通過反複清洗,並在高質量的純水加超聲波中長時間(jiān)浸(jìn)泡來得到。但是,工模的清洗就不(bú)同,尤其是一些熱做模具(jù)鋼,如果(guǒ)像裝飾塗層那樣去清洗,就會鏽得(dé)一塌糊塗。 由於工模塗層(céng)的原始表麵狀態,除了一(yī)些高標準的(de)鏡麵模具以外,一般較裝飾塗層(céng)要粗糙,因而,對塗層(céng)後的表麵狀(zhuàng)態(tài)的要求也不象裝飾塗層那樣高,這就允許我們采取快速過水,用幹燥、無油(yóu)的(de)壓縮空氣吹幹,然後對(duì)工模(mó)強風幹燥的方法來處理。而那些高標準的(de)鏡麵模具(jù),一般均為136 等不鏽鋼,可以借用裝飾塗層的清洗法。 總而言之,工模塗層前的清洗方法因工模所使用的材料(liào)的不同而不同,因工模塗(tú)層前的表麵狀態(tài)的不同而不(bú)同,且不可千篇一律(lǜ)。下麵(miàn)是幾種材料生鏽由難到易的(de)排序,供(gòng)參考:
不(bú)鏽鋼、硬質(zhì)合金、金屬陶瓷合金、DC53、高速鋼、8407 有一種自動清(qīng)洗機型號為 CR288,產自德國。該機一(yī)次最大 清洗量為 80KG,主要用於清洗(xǐ)刀具、小型零部件、或(huò)小尺寸的模具。它共有三個清洗缸,裏麵的溶液分(fèn)別為自來(lái)水+清洗劑、自(zì)來水、去離子水。除了常見的超聲波(bō)、大水衝洗、噴淋、擺(bǎi)動、熱風幹燥(zào)等功能(néng)外,該機另外一個優點是最後設有(yǒu)抽真(zhēn)空步驟(zhòu),可以使水分盡快揮發掉。 自(zì)動清洗機內存十(shí)種工藝,均由供方預(yù)先設定。一至九可分(fèn)別用於不同類型的產品、不(bú)同的表麵狀態的淨化處理。第十種用於加注清洗劑。 4.2.3 噴砂 噴(pēn)砂法(fǎ)是借助壓縮(suō)空氣使磨料強力衝刷工件表麵,從而去(qù)除鏽蝕、積碳、焊渣、氧(yǎng)化皮、殘鹽、舊漆(qī)層等表麵缺陷。按磨料使用條件,噴砂分為幹(gàn)噴(pēn)砂與濕噴砂兩類。 噴砂的工藝參數主要有槍距、傾(qīng)角、裝夾(jiá)台旋轉速度、移動速度、行程、往返次數、噴砂(shā)時間、噴砂氣壓。我(wǒ)們已使用過的參數有(yǒu)槍距:30~70mm; 傾角 30~70?C; 裝夾台旋轉速度 10~30;往返次數 3~9 次(cì);噴砂氣壓:1.8~3.5 巴等。具體操作時,根據工件(jiàn)表麵髒(zāng)汙程度(dù),工件硬度,工件表麵幾何形狀等因素,選取上下限。我們在幹噴(pēn)砂(shā)機中所選用的磨料為(wéi)玻璃珠,適合噴一些硬(yìng)度介中(zhōng)的材料,如油鋼、模(mó)具等;在液體噴砂機中所選用的磨料為氧化鋁,硬度較高,適合噴一些硬度高的材料,如硬質合金材料。對於工模塗層而言,噴砂(shā)所使用(yòng)的磨料粒度(dù)也很重要。如果磨料粒度過大,則工件表麵太粗糙;如果磨料粒度太小,又(yòu)會降低衝擊力度(dù),甚至嵌在工件表麵,清洗難(nán)以去除,從而使工件塗層附著(zhe)力降低。為此(cǐ),歐洲一些國家,對工模塗層前噴砂 所用磨料粒度做過仔細研究,嚴格到必(bì)須保(bǎo)證 85%以上的晶粒度在中 A、B 兩點範圍內才能使(shǐ)用。相比之下,我國磨料的供應(yīng)商還缺乏這方麵的共識,我們(men)也很少有做(zuò)這方麵的檢驗。 4.3 PVD 塗層工藝(加熱、離子清洗、塗層、冷卻、工藝氣體、氣壓、溫(wēn)度、濺射功率) 4.4 FQC FQC 的英文(wén)全拚(pīn)為:“Function Quality Control”,意思是功能(néng)質量控製(zhì),它有別與一般意義上(shàng)的(de) OQC(Out Quality Control) 。FQC 的內容主要包括外觀檢查(chá)、層(céng)深檢(jiǎn)查(chá)、附著(zhe)力檢查、耐磨性檢查、抗(kàng)蝕性檢查、模擬性測試等方法。我廠目前應用的(de)主要有外(wài)觀檢查、層深(shēn)檢查和附著力檢查。由於我們所接觸的(de)產品大多都是不允許做破壞(huài)性檢查的,因而我們在鍍膜時,每批都(dōu)會放進(jìn)隨批試(shì)樣。做層深檢查和附著力檢查的時候,大多數情況下,實際上是對隨批試樣進行檢查。因為試(shì)樣與產品在原(yuán)材料、熱處理狀態、裝夾位置等(děng)方(fāng)麵都難於一致,所以這(zhè)樣檢測出的結果,與產品實際值會有一定的(de)誤差。有時可能還會有相當大的誤(wù)差,隻能做參考使用。當然,必要的時候(hòu),我們也(yě)可以通過製作模擬件,達到準確測(cè)量的目的。
4.4.1 外觀檢
對於開門取件後的產(chǎn)品,應仔(zǎi)細檢(jiǎn)查表麵(miàn)有(yǒu)無裂紋、掉塗層、疏鬆等缺陷。對於刀具、刀粒,還需在顯微鏡下仔細檢(jiǎn)查它(tā)們的刃口狀態。 4.4.2 層深檢查 層(céng)深檢查有切片金相觀(guān)察法、X-ray 檢查法、用單色光做光源的光學測試法、球磨儀測試法等多種方法。工模塗層的層深檢查是在(zài)球磨儀上進行的。方法是先(xiān)用直徑為(wéi) 10mm 的鋼球與測試表麵滾磨,然後(hòu)在(zài)顯微鏡下測量磨痕的有關(guān)數據,帶入公式中,即可方便算出層深。 這種層深檢(jiǎn)查法的特(tè)點(diǎn)是(shì):方便適用,誤差稍(shāo)大(dà)。但這種誤差(chà)應用於工模上麵影(yǐng)響不會太大。有(yǒu)興趣(qù)的同事還可參閱有關的說(shuō)明書。附著力的檢查方法有很多,各個廠根據自己產品(pǐn)的特點,都製定了相(xiàng)應的檢(jiǎn)測(cè)方法。其中,比(bǐ)較權威的方法有兩種,一種是(shì)在洛氏硬度計上,以圓錐型金剛石壓頭(tóu)做壓痕試驗,在顯微鏡下觀察,以壓痕周邊裂紋的多少來判斷塗層(céng)附著力的高低。該方法對(duì)金剛石壓頭的形狀要求很高,不但嚴(yán)格要求中心點在圓的中心,而且金剛石圓錐的圓度必須十分規則。遺憾的是,目前,我國還沒有它的國家或行(háng)業標準;另一(yī)種方法是劃痕法,我國有些塗層發起較早的科研部門,也是采用的該方法,有專門的國家行業標(biāo)準可供查(chá)詢。 5. 工裝夾(jiá)具的處理 6. 塗(tú)後處理工藝(噴(pēn)砂、塗脂技術,拋光(guāng)處理) 7. 檢測(cè)技術(結合力的檢測、層深的檢測、酸蝕(shí)) 8. 塗層剝(bāo)離技術(TiN/TiAlN 的剝離(lí)技術、CrN/DLC/CrAlTiN 的剝離技術、硬質合金的表(biǎo)麵(miàn)塗層剝離技術) 9.塗層(céng)刀具的應用技術(塗層的正確選(xuǎn)擇、塗層刀具的正確使用 塗層對刀具的優化非常大,由(yóu)於高速切削加工比傳統切削加工所產(chǎn)生的溫度要高,應用塗層,可以發揮其耐高(gāo)溫、抗氧化及加硬材質等作用。例如,氮化鉻(CrN)塗層可降低磨擦係數,改善光潔度及排屑(xiè)情況
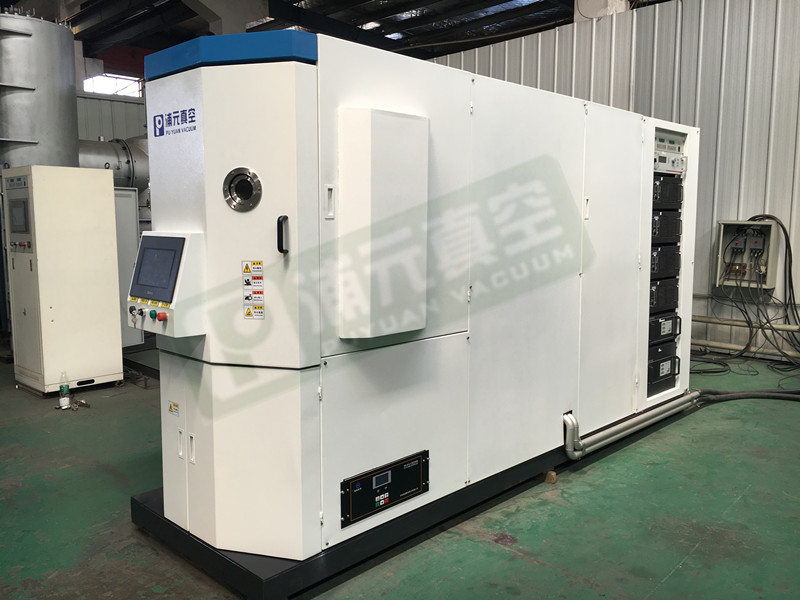